21년 4개 공정모델 개발에 9개 기업, 13개 실증, 23년까지 총 19개 공정모델 개발·보급
제조공정에 첨단로봇 채택한 기업들 생산성·품질관리·가격경쟁력·작업·근로환경 크게 개선
산업부는 2019년 ‘제3차 지능형 로봇 기본계획’을 발표하고, 근무 환경이 열악한 섬유·뿌리·식품 등 3대 제조업을 중심으로 제조로봇 보급 확산사업을 추진하고 있다.
이에 따라 섬유산업 등 3대 제조업을 중심으로 로봇 도입이 필요한 108개 공정을 우선 선별해 업종별·공정별 공정모델 개발 및 실증사업을 추진하고 있다.
한국섬유기계융합연구원(원장 성하경, KOTMI) 기계로봇연구센터(센터장 이재용)는 한국로봇산업진흥원(원장 손웅희, KIRIA)이 주최하는 ‘2021년 지능형로봇 보급 및 확산사업’의 섬유산업분야를 맡아 제조로봇 도입 지원컨설팅 및 경제성 분석을 통해 섬유산업 공정모델을 대상으로 제조로봇 도입을 지원하고 있다.
2020년에 4개 공정모델(보빈 탈장착, 원사시험/검사 보조, 원단 롤이송, 가죽이적재)에 6개 수요기업을 대상으로 6개 공정을 실증완료 했으며, 2021년에는 4개 공정모델(보빈 이송/적재 공정, 용액 공급/투입 공정, 제품 픽업/이송 공정, 제품 포장 공정)을 대상으로 9개 수요기업에 13개 공정을 실증완료 했다.
자동차, 철강, 전기/전자산업에 비해 상대적으로 로봇 도입이 미미했던 섬유산업은 제조로봇 실증 지원사업을 통해 섬유현장 채택 사례가 만들어지고 있으며, 2019년부터 2023년까지 5년 간, 총 19개 공정모델을 개발·보급 예정이어서 향후 다양한 공정으로 확대될 전망이다.
한편, 2021년 9개의 섬유기업(삼환염공, 시마, 대방, 대영합섬, 삼우텍스텍, 삼덕섬유, 유진한일합섬, 유일코퍼레이션, 코리아 마스크)에 채택된 13개 공정의 실증사례를 소개한다.
■ 유진한일합섬(도입) – 테크원코리아(공급)
경남 의령에 위치한 유진한일합섬(대표 이인수)은 아크릴 섬유를 최초로 생산하기 시작, 스펀본드 부직포 및 특수사를 개발·생산하는 대표적인 섬유기업이다.
부직포 롤 포장 및 이송 공정은 부직포 비닐 포장 → 사이드 테이핑 → 이송 → 적재의 순서로 진행되며, 유진한일합섬에서는 부직포 이송, 적재 공정에 보빈 이송/적재 공정(‘20년 개발 공정모델)을 도입했다.
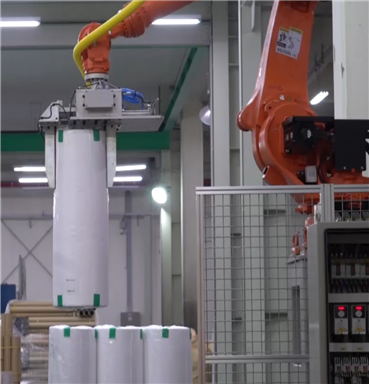
▶ 유진한일합섬 TO BE
공급기업 테크원코리아(이시진 대표)는 롤 실링 및 이송공정을 6축 다관절로봇과 여러 자동화 보조 장치를 활용한 자동화 시스템을 구축했다.
달성성과로 인적 실수 및 다양한 요인에 의해 발생하는 불량을 0.25%에서 0.124%로 감소한 50.4%의 불량률 감소를 보였으며, 롤 밀림현상이 해결되어 1일 생산량이 12.5회/hr에서 15.1회/hr로 증가해 생산성이 20.8% 향상됐다.
유진한일합섬 정용식 상무는 “로봇 도입으로 작업자의 근골격계 산업재해에서 벗어나게 되어 피로도가 줄고 작업 효율이 상승했다”고 평가했다.
■ 유일코퍼레이션(도입) – 제팩(공급)
경북 성주군에 위치한 유일코퍼레이션(이인숙 대표)은 홈인테리어용 원단 생산 전문 업체이다.
보빈 이송 및 적재 공정은 보빈이송 → 보빈적재 → 스티로폼 제거 순으로 이루어지며, 유일코퍼레이션은 보빈 이적재 작업에 보빈 이송/적재 공정(‘20년 개발 공정모델)을 도입했다.
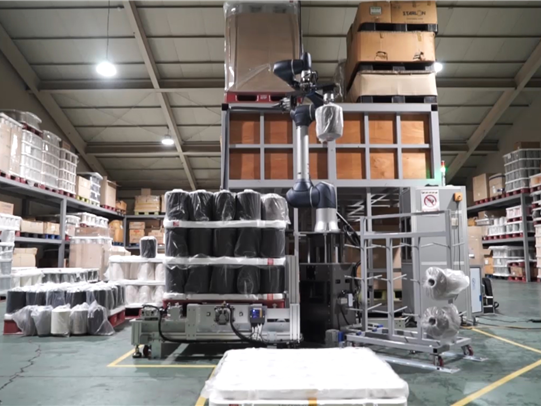
▶ 유일코퍼레이션 TO BE
공급기업 제팩(이준제 대표)은 협동로봇을 활용해 보빈을 피킹, 크릴의 알맞은 위치에 보빈을 적재하고, 한 층의 모든 보빈이 이송 완료되면 그리퍼를 교체해 스티로폼 패드를 제거하는 작업을 반복적으로 수행하도록 보빈 이송/적재 시스템을 구성했다.
달성성과로 작업자의 실수로 보빈이 크릴 봉에 부딪히거나 손에서 놓쳐 발생하는 오염 또는 손상 등의 불량이 10%에서 7.7%로 줄어 23%의 불량률 감소를 보였으며, 인건비 절감을 통해 원가를 월 700만원에서 월 350만원으로 50% 감소시켜 가격경쟁력을 얻었다.
유일코퍼레이션 류준상 이사는 “로봇 투입을 통해 인력을 줄이고 근로환경의 개선으로 근로자들의 만족도가 높아졌다”고 말했다.
■ 시마(도입) – 포원시스템(공급)
경북 영천시에 위치한 시마(대표 김지미)는 복합방적사 및 아라미드와 같은 특수섬유를 수요처의 요구에 따라 생산하는 업체이다.
시마에서 수행하는 목관 교체 공정은 목관제거 → 목관적재 → 새 목관 장착 순으로 진행되며, 시마는 목관 이송/교체 공정에 보빈 이송/적재 공정(‘20년 개발 공정모델)을 도입했다.

▶시마 TO BE
공급기업 포원시스템(대표 권오대)은 인력 고령화로 작업성 저하 및 과로의 문제를 해결하고자 레일과 6축 다관절로봇을 이용한 목관 자동 교체 시스템을 시마가 도입했다.
달성성과로 1일 생산량이 7,020kg/day에서 8,757kg/day로 증가해 생산성 24% 향상됐으며, 제품의 원가는 1,500만원/월에서 750만원/월로 감소해 원가를 50%가량 절감하는 효과를 얻었다.
시마 김지미 대표는 “제조로봇 도입을 통해 3교대의 작업을 1명이 수행 가능하게 됐으며, 기존 인력의 효율적인 업무 배치를 통해 근무만족도가 향상됐다”고 밝혔다.
■ 삼환염공(도입) - 포원시스템(공급)
대구광역시에 위치한 삼환염공(안훈주 대표)은 Nylon 및 Polyester직물의 염색, 가공 및 코팅을 전문으로 생산하는 업체이다.
일반적인 염색공정은 염료 준비 → 염료 이송 → 염료 투입 순으로 진행되며, 삼환염공은 염료이송 및 투입 작업에 용액 공급/투입공정(‘20년 개발 공정모델)을 도입했다.
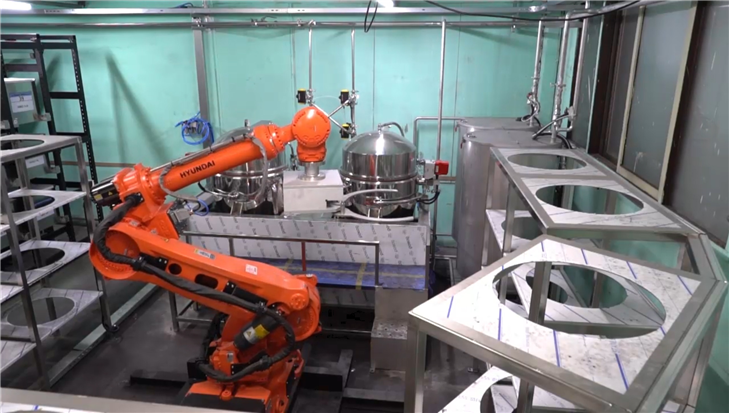
▶삼환염공 TO BE
공급기업 포원시스템(대표 권오대)은 작업자의 노동력을 중심으로 이루어진 공정에 다관절 로봇을 도입해 용기 투입부터 거치, 로딩 및 배출까지의 전 과정을 자동화시켰다.
달성성과로 1일 생산량은 43,760개에서 69,310개로 증가해 생산성이 58.3% 향상됐으며, 불량은 5%에서 1.4%로 감소해 도입 전 대비 불량률이 72% 감소했다.
삼환염공 안훈주 대표는 “고령의 노동자들에게 고중량의 염료이송을 통해 생기는 근골격계 질환 및 염료비산을 통한 호흡기 질환 등의 문제점을 로봇시스템 채택으로 작업자의 노동환경 개선에 탁월한 효과를 가져왔고 쾌적한 작업환경 구축에 큰 도움이 됐다”고 밝혔다.
■ 코리아마스크(도입) – 로엔(공급)
경기도 파주시에 위치한 코리아마스크(대표 안현)는 일상의 유해 물질로부터 사람을 보호하는 보건/방역 마스크 개발 및 생산업체이다.
마스크 포장 공정은 마스크 파우치 이송 및 실링 → 파우치 카운팅 → 박스 포장 → 컨베이어벨트 이송 순으로 진행되며, 코리아마스크는 마스크를 이송·포장하는 공정에 제품 포장 공정(‘20년 개발 공정모델)을 도입했다.

▶코리아 마스크 TO BE
공급기업 로엔(대표 김상락)은 수작업으로 이루어지는 마스크 파우치 카운팅 및 박스 내 인케이싱 공정에서 작업자의 숙련도 차이와 실수로 인해 발생하는 불안정성을 해결하고자 6축 다관절로봇을 이용한 자동화 시스템을 코리아마스크에 도입했다.
달성성과로 작업자의 카운팅 실수로 발생하는 공정 불량은 3%에서 0.5%로 줄어 불량률이 83.3% 감소했다.
또한, 작업자의 숙련도 편차에 의한 생산량 불균형이 제거되어 1일 생산 데이터의 확보 및 생산량이 1,040개에서 1,215개로 증가해 생산성이 16.8% 향상됐다.
코리아마스크 안현 대표는 “생산량 데이터의 확보에 따라 계획 및 일정을 수립할 수 있게 됐으며, 수량 오류에 의한 고객 클레임이 제거됐다”고 말했다.
■ 대방(도입) - 대동정공(공급)
경남 양산에 위치한 대방(대표 김명선)은 열가소성 hot melt 및 습기 경화형 hot melt로 자동차 내장재 및 산업용 자재를 생산 공급하는 업체이다.
가죽 접착공정은 표면 코팅기에 스펀지를 투입 → 코팅 된 스펀지 수거 → 가죽 이송 및 접착의 순서로 진행되며, 대방은 스펀지와 가죽을 이송하고 접착하는 공정에 제품 픽업 이송(‘21년 개발 공정모델)과 가죽 이적재 공정(’19년 개발 공정모델)을 도입했다.

▶대방 TO BE
공급기업 대동정공(대표 이상환)은 소재공급 지그, 6축 다관절로봇 및 비전 검사 직교로봇 유닛을 이용해 가죽 이적재 및 접착 자동화 시스템을 구축했다.
달성성과로 작업자가 접착을 위해 장시간 같은 자세를 유지함에 따라 발생하는 근골격계 질환 발생을 예방할 수 있게 됐고, 1일 생산량은 1인 기준 1.04개/min에서 6개/min으로 증가해 생산성이 477% 향상됐으며, 불량 또한 3%에서 0.82%로 감소해 불량률이 72.6% 감소했다.
대방 강성원 이사는 “작업자의 노동 강도 감소, 불량률 최소화, 일정량의 제품 생산을 통해 품질관리에 집중할 수 있어 고객사의 신뢰도가 향상될 것으로 기대된다”고 말했다.
■대영합섬, 삼덕섬유, 삼우텍스텍(도입) – 하이젠모터(공급)
대영합섬(대표 이민수), 삼우텍스텍(대표 박철우), 삼덕섬유(대표 최만식)는 폴리에스터 복합사를 고객 맞춤 가공방식으로 생산하는 기업이다.
일반적으로 원사 가공 후 원사 이송 → 원사 비닐 포장 → 원사 적재 → 원사 팔레트 래핑 포장 → 포장 완료 원사 배출의 순으로 진행되며, 위 3개 기업은 이송/비닐 포장/적재 및 래핑 포장/배출에 제품 픽업 이송(‘20년 개발 공정모델)과 제품 포장 공정(‘20년 개발 공정모델)을 도입했다.

▶대영합섬/삼우텍스텍/삼덕섬유 TO BE
공급기업 하이젠모터(대표 김재학)는 6축 다관절로봇과 주변 장비들로 원스톱 라인을 구현했다.
제품 픽업 이송 라인에 원사 개별 무게 측정 장치와 개별 비닐 포장 장치를 개발 및 설치해 무게 오측정과 비닐 포장 실수 불량을 줄였고, 제품 포장 라인에 멀티 그리퍼를 개발해 다수의 원사를 한 번에 그리핑이 가능하게 했다.공정별로 원사 픽업 이송 시스템에 가반하중 20kg의 6축 다관절로봇(현대로보틱스, HH020) 2대와 주변장치, 원사 포장 시스템에 가반하중 220kg의 6축 다관절로봇(현대로보틱스, HS-220) 1대 및 주변장치를 도입했다.
원스톱 라인 도입으로 원사 투입, 품질검사(중량), 적재, 포장 및 배출 작업을 모두 자동화했다.
달성성과로 ‘대영합섬’은 생산성이 231,314kg/월에서 289,154kg/월로 증가해 생산성 25% 향상과 원가가 74,630천원에서 49,753천원으로 줄어들어 33.3% 원가절감을 나타냈다.
‘삼덕섬유’의 생산량은 291,902kg/월에서 343,636kg/월로 증가해 17.72%의 생산성 상승과 불량이 0.5%에서 0.4% 미만으로 줄어 불량률이 20% 감소했다.
‘삼우텍스텍’은 생산량이 259ton/월에서 320ton/월로 증가해 22.4%의 생산성이 상승했다.
원가는 74,630천원에서 49,753천원으로 33%의 원가가 절감됐으며, 고객 납기 준수율이 기존보다 15.4% 증가해 97%의 상승률을 보였다.
대영합섬 문영주 소장은 “제조로봇의 도입으로 근로환경 개선과 인력 재배치로 제품의 원가절감 및 가격경쟁력이 강화됐다”며, “섬유산업의 첨단화에 한발 더 나아가는 계기가 돼다”고 평가했다.
삼덕섬유 최만식 대표는 “수작업을 로봇으로 대체해 근로자들의 노동 강도가 줄고, 생산성이 향상 됐다. 무엇보다도 품질관리 향상으로 인한 기업 이미지 상승효과가 있어 인재 채용의 한계를 해결하는 데 큰 도움이 됐다”고 말했다.
<김진일 기자>
Comments